立体成型注塑模具局部收缩工艺分析
R.A.Harris
H.A.Newlyn
P.M.Dickens
R.J.M.Hague
摘要:利用立体光刻成型技术(SL)可以缩短模具的生产周期,使塑料制件能够快速成型。 该工艺的优点是在制造零件时与传统的制造方法相比能够节省时间和成本。
除此以外,立体光刻成型工艺的收缩变形率与常规的成型工艺相比有很大的改善,这些特点主要是是体现在利用立体光刻成型的注塑模具成型工艺与传统的生产工艺相比有很大的不同之处。
利用立体光刻成型工艺模具的生产与铝模的生产在收缩率上存在不同,实验中,利用两种不同的聚合物和模具结构,采用相同的处理方式,使模具的传热性作为是实验的唯一变量来加以衡量。
该实验表明在两种不同的模具材料在不同温度分布下的收缩率变化情况。收缩率的变化情况必须得到补偿以确定模具零部件的总体收缩变形情况。补偿的方法是通过数学方法和利用模型有限元翻译。两种技术取都决于成型期间的受热情况。这些受热情况通过实时数据采集和有限元分析模拟成型。研究结果应用提供了涉及到模具材料及聚合物使用所引起的收缩率变化的整体情况,这将使零部件几何形状的生产更加准确。
关键词:有限元分析;注塑成型;聚合物收缩;快速模具及立体成型。
1.引言
立体光刻成型技术(SL)已经可以直接的生产用于注塑成型的模具腔(插入)。精确的立体光刻成型工艺需要注塑成型前注入环氧。该工艺为快速模具成型提供了途径,依靠几何复杂性和聚合物造型,可以生产高达约50个零件[ 1 ] 。利用立体光刻成型能够使多种聚合物被成功地塑造成注塑模具。这些聚合物包括聚酯(PE),聚丙烯(PP),聚苯乙烯(PS),聚酰胺(PA),聚碳酸酯(PC),聚醚以太酮(PEEK),丙烯腈-苯乙烯-丙烯酸酯(ASA)的丙烯腈-丁二烯-苯乙烯(ABS)。
立体光刻成型生成的环氧模腔与金属模具相比具有不同的热性能。由于模具材料固有的传热性能,对于不同的材料的模具其加热或冷却的速度也有很大的不同之处。许多聚合物的收缩率不同是由于在造型期间的冷却条件不同而引起的。该研究表明了受热条件对模具局部材料收缩的影响情况。
2.目的
这项研究的目的是旨在评估用立体光刻成型模具制造与金属快速模具制造在注塑成型时的收缩情况。
3.工艺分析
3.1实验设计
实验的目的是确定两聚合物(聚酰胺66 [尼龙66,结晶]和丙烯腈-丁二烯-苯乙烯[ ABS的,无定形])在不同材料(光固化成形[SL]和铝[AL])的注塑成型在48小时的收缩特性。这将要直接比较成型腔和模压零件的尺寸情况。
除了热塑性高分子材料和工具材料的选择,注射成型的收缩问题还部分的决于几个过程变量,注塑压力,机器型号等。然而 ,在这两个试验集(尼龙66 & ABS)中的唯一变量分别是刀具材料的类型(SL&AL)和刀具几何型腔(bar & disc—这些被用于根据聚合物流向辨认造型期间的收缩情况,在3.2中进一步解释 )。就该注塑成型而言,唯一有影响的变量是在每次实验时SL和铝模的热性能。 这取决于注入聚合物进行脱离模压部分通过腔用料是的导热系数。模具材料的导热性有很多的不同之处 :SL=0.2 W/m/K,AL=200 W/m/K。
3.2 模具设计
模具设计是根据布的EN ISO 294 - 1和4 [ 12,13 ]和ASTM D955 [ 14 ]建立的注射成型聚合物收缩标准而设计的。
样本的两种不同的结构造型是为了提供与该目录聚合物流同步的平行(纵向)和垂直(径向)两个方向的收缩测量。这些模具型腔的三维图像可以看作如图1所示 。
使用草案角度,以纾缓部分移离模具为1.5 °,该值此前被证明是一个为减少由立体光刻成型的模具零部件潜在的损害最佳值 [ 15 ] 。
浇道口的设计是为了使得所设计模具能够避免可以破坏立体光刻成型模具的热量和压力,浓度(如范浇注)。使用该浇注系统是为了确保注塑过程中模具内的各部分之间无大的压力差异,也可防止模具注射压力不均所造成的过早冻结中断浇道的现象。
浇道口的深度是与横截面宽度尺寸(disc&bar)相同 。一般情况下浇道口宽度的大小正比于型腔尺寸的大小。
模具并不包括局部注射系统。刚性喷射器将提供与其他区域不同的注射速率使成型腔区域的热传递速率高于其它区域。钢的导热性比SL高的多,但却没有AL的导热性的导热性好。这不能够用实验来全面的估计SL或AL模具所提供的热传递在局部收缩问题上的影响。注塑制件形状简单的的模具用手动就可以轻易地被去除由于没有喷射器系统所引起的问题。
立体光刻模具是由具有三维系统的sla350机用vantico5190树脂加工成型的。树脂建设层厚度为0.05毫米,因为这是以被证明了可以延长立体光刻模具的工作寿命 [ 16 ] 最佳值。
为了提高成型质量,在入口处插入一些摇枕。这些摇枕便于对齐使机器压板对齐,保证塑料经锥形浇道进入模具,同时也保护了刀具,防止过度的施加压力。
3.3 模具温度记录
为了确立每套模具都存在的传热特性,需在整个成型周期内插入K型热电偶以便记录温度。热电偶的上表面一般位于成型面下0.5毫米的表面。每对热电偶在插入之前需对其各自的标值进行检查。在插入到模具内以后,通过0.5毫米型腔下表面热电偶温度的变化来反映型腔内的温度变化情况。热电偶测量的温度所与实际表面的温
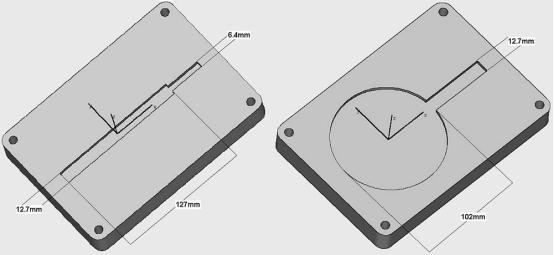
(图1)
度的差别不能大于± 1 °。钙数据采集程序记录,并记录温度分布超过10 分钟的时间内,在成型中的一部份。利用数据采集程序对零件在造型期间10 分钟时间内内的温度分布情况进行记录。
3.4注塑成型
为了消除额外的实验变量,重要的是要找到两聚合物总体参数值,以及模具的形状和模具的材料类型。其它用于补偿纵向和径向部分的所有几何参数均是通过实验获得的。
在尼龙66中的A70NAT是由聚乙烯生成的。将超光滑的ABS 2373条应用于径向定量浇铸系统. 两种聚合物都具有吸湿性,需要在干燥处理之前进行加工。
该注塑机使用的是BF 600/125 CDC模型与UL4000人工控制单元。该注塑机是由一个60吨液压夹紧装置和一个带有传统锥形喷嘴的125 × 35毫米往复螺杆注射装置所组成的。其工艺参数如下列所示:
●熔体温度定在270 ° C时,在每5个桶温度区。
●注射速度为100毫米/秒。
●喷射压力为150巴。
●后续压力为150巴,保持3秒钟, 100毫米的余量。
●模具注射之前的环境温度为23.5 ° C。
●局部冷却时间不超过40秒,该时间是确立在不会引起工件局部滑移失真的条件上的。
●锁模力为15吨。
3.5 收缩测量
BS EN ISO 291[17]被用来作为是零件的成型环境和48h后检测的标准。注塑成型后的模腔及模具样本的实测值与给定的理论值相差近0.01毫米。许多零件的成型数据都是由多次实验和测量而决定的。零部件和型腔的长度尺寸大否需要测量。浇道口位于模具的中央,也可以放在成型件的一侧。模具零件的径向长度测量值及几何形状如图2所示。
测量出样件型腔尺寸于实际成型腔的差值百分比,以便扩大模具热补偿。
4.结果分析
4.1.模具温度廓线
有关数据显示,两种类型的聚合物( ABS&PA66 )和两种几何型腔(bar&disk)之间的温度分布具有很大的相似性(不大于± 5 %的差异)。立体光刻成型模具和铝模具具有不同温度轮廓线。不同材料的成型方式反映时间与温度之间关系的轮廓曲线如图3所示。概括说明SL和铝模具成型时温度的不同点。铝制模具由于其材料具有较高的导热性,其温度轮廓线变化较快。SL模具温度变化较为缓慢,在没有外在条件帮助(由压缩空气冷却)的情况下,需要15分钟才能冷却至常温。
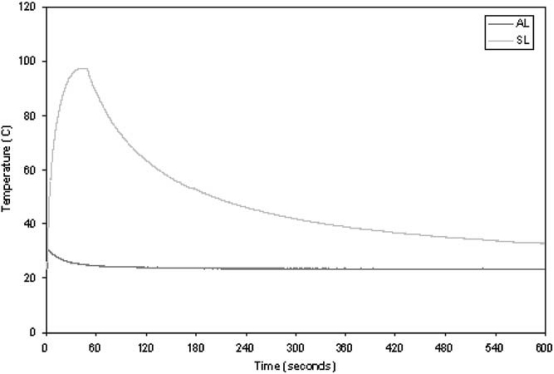
(图3)
4.2 初始收缩结果
初始的收缩值,是由如表1所示的零件/模具的测量结果计算得到的。不过,这些数字还需要进一步考虑总体收缩问题的发生. 这些将在下文阐述。
4.3热膨胀补偿计算
两种模具材料的热膨胀补偿计算可以用同一种方法,尽管各方面的参数不同。模具及零部件的收缩在测量时必须要进行误差补偿,以确定与其真实数值的差别。更正零件收缩的方法就是扩大相对应的模具数值。
扩大了模具的数值将会导致型腔受到扩张,而不是收缩。这说明测量模具型腔的在标准温度为50 ° C,需要保持10分钟左右(参见图2)。这些将在后面加以证明(第4.4.5节)。
用Sm对由模具热膨胀而引起的局部收缩进行修正,其方法是:DSm=am(Tm-Ta)[13],其中:am为模具材料线性膨胀系数 ,Tm为模具注射期间的最高温度,Ta为注塑机上的温度。
一般应用为:
am
●SL=59×10-6 m/m/K
●AL=23.8×10-6 m/m/K [18]
Ta:
●SL=23.5°C
●AL=23.5°C
它们各自的意义在3.4节已经加以说明。
Tm:
这些数值的使用是由以往模具注塑温度和注塑参数经计算得来的的,在该温度点时聚合物停止流动。该压力点的应用将对收缩有影响。在模具进一步受热膨胀时将无法影响其数值如图四所示。不同模具的最高温度为:
●SL disc=57.46°C
●SL bar=44.37°C
●AL disc & bar=30.39°C
立体成型模具的注塑周期要在交长堵塞时间内完成,使的温度持续上升。由于不同的需要,disc&bar两种模具的最高注塑温度也不同。
因此,各类模具的热膨胀系数计算结果如下:
SL disc mould=59×10-6 (57.46-23.5)
=2.00364 mm/m
=0.200364%
SL bar mould
=59×10-6 (44.47-23.5)
=1.23133 mm/m
=0.123133%
AL disc&bar mould
=23.8×10-6 (30.39-23.5)
=0.16422 mm/m
=0.016422%
这些实测的收缩百分比可以计算出总收缩率,便于模具的热膨胀补偿。这些数值如表1所示。此外,计算也比较简单。假设模具的温度是整体上升的话,那么通过数据采集工具就可以进行很好的处理。而实际上模具地温度是呈局部上升的。因此就需要进一步的的弄清模具型腔发生膨胀是的温度分布情况,以便进行补偿。
4.4热膨胀补偿-有限元分析
有限元分析(FEA)用于因型腔内温度不均匀而引起的模具热膨胀分析。有限元分析软件用在这方面的主要是算法。有限元分析有两种方法。一是分析模具的瞬态热,以确定温度的分布情况。二是对温度分布的结果进行线性分析,以确定模腔热膨胀系数。
4.4.1. 有限元分析.步骤 1 -建立模型
有限元分析首先需要创建有限元模型和有限元网格。为了减少分析方案的时间, 每个试样均由模具制造快速。这些如图5所示。
挤压这种网格模型间距的间距每个节点为0.5毫米,在当前区域成型腔下方( 〜 4毫米深),这能够很好的分析型腔的热膨胀问题。这些节点相当于热电偶在试验
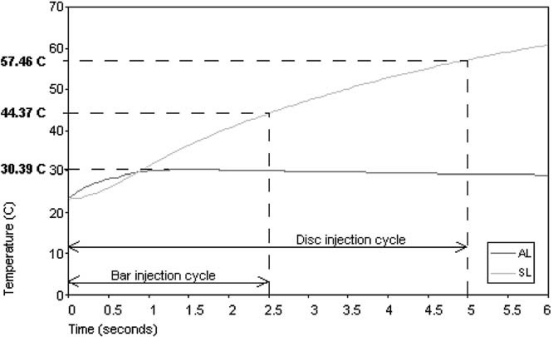
(图4)
中的温度变化情况(见3.3节)。其余模型的网格间距为10毫米左右以在更短的时间里进行有限元分析。
4.4.2. 有限元分析. 步骤2 -配置材料
该材料被假设为理想均质独立同性恒温材料。起具体数据如表2所示。
4.4.3. 有限元分析.步骤 3 -瞬态热分析
瞬态热分析指的是在同一温度情况下的时间函数。通过实验对模具的有关条件进行分析。
由注塑时产生的能量(热量)被传散到周围的模具材料。这些热量是有限的,聚合物的温度在减少,其热量被传递到温度较低的模具中。
通过有限元瞬态热分析,可以得出以下的结论:
●聚合物被注入模具时的起使温度是270 ° C。
●塑料和模具之间无热敏阻力。
●模具材料的起使温度是23.5 ° C。
要对一些重要温度数据(参见图4 )的实验结果进行有限元分析,并采用正确的步骤进行解决。
根据所调查的模型发生变化(膨胀)是温度的分布情况,选定一个条件(温度),在规定的时间就可作进一步的线性弹性分析。
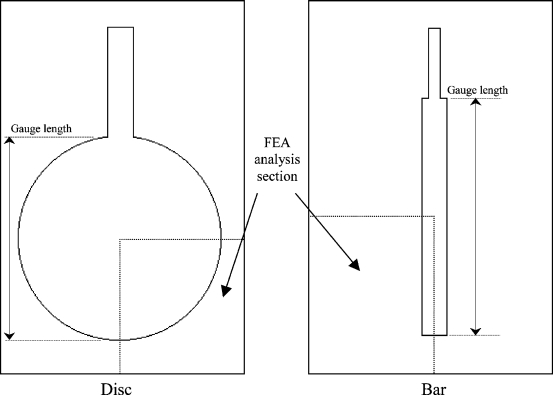
(图5)
4.4.4. 有限元分析. 步骤4 -线性弹性分析
该模型在有限元模型设计(如图所示,在图5)的基础上很好的解决了注射口对称性问题。其没有规定的限制,允许自由的选用。该方法应用较多,因为有助于增强模具的注塑能力。不过,已经表明,即使在最佳条件下,任意方向的热膨胀最大值是0.25毫米。应用该数值有助于优化模具的整体结构。其具体情况如图6所示。
4.4.5. 有限元分析. 步骤5—结果
该模型经线性弹性分析后,其模型的热膨胀问题主要是取决于型腔厚度的大小。具体的情形如图7所示。
根据这些起平均运动速度(扩大)就可以确定起数值了。每一种情况都可表明型腔外扩情况。确定共模扩张的测量数值是位移矢量一倍,因为轴向扩张的方向成型方向相反。引起这些扩张结果的局部收缩值如表1所列 。
5. 讨论
从结果(表1 )可以看出,为了消除局部收缩,对所有的聚合物/工具组合进行热补偿是很有必要的。同是也获得了不同收缩值的模具扩张补偿值。有限元分析解决问题比单纯的计算法更为优越。采用该方法可以准确的分析模具热膨胀和局部收缩问题。应该指出的是,有限元分析法是一种近似解法,并需依靠精确的模型,网格密度
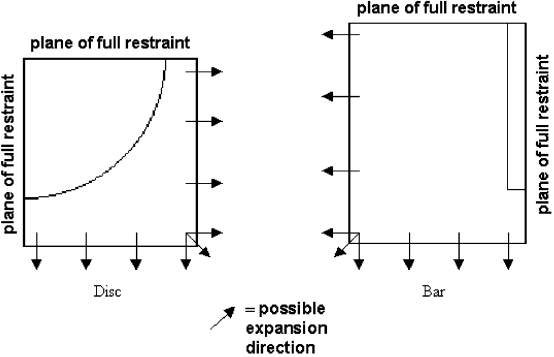
(图6)
大,且对材料性能、表面摩擦力和自体约束也有很高的要求。虽然大多数的有限元分
析较为确切,但生产实际中有些项目的分析结果仍还需作必要的修改。
热膨胀补偿包括以下关于收缩几个主要问题。主要包括:
5.1.收缩方向
液晶聚合物(PA66)在聚合物流动方向(轴向)垂直聚合物流向(径向)上具有较大的收缩性差异(达 7 %以上)。部分非晶聚合物(ABS)也或多或少有些差异(达3%以上)。这些是所有注塑成型零部件的典型特征,晶体零件更容易由于聚合物[ 19 ]受到不同流动方向(定向分歧)而造成更大的偏差。
5.2.模具材料尼龙66的收缩
模具材料-尼龙66 收缩结果表明,这种收缩发生在尼龙66部件,立体成型模具比铝模具高出一倍。预计尼龙66收缩幅度为1-2.2 % [ 20 ] 。铝模的零件收缩率仅略高于最低预期数值,而立体成型模的零件收缩率最高可超过预期的收缩幅度。各种零件的大小也可用ABS零件来衡量。尼龙66零件在0.35毫米〜 0.18毫米范围的测量不同于ABS零件。这是晶体高分子材料的典型特征,于无定形聚合物相比[ 21 ] 很难保持零件的尺寸公差。
5.3.模具材料ABS的收缩
研究结果表明, ABS零件的收缩不受模具材料的限制。ABS零件的收缩实验值为0.76%。ABS预期收缩幅度为0.5-0.6%[ 20 ] 。
6. 结论
研究表明,尼龙66 (一种结晶聚合物)在立体成型模具中注射成型收缩率是铝模具的两倍。在同一实验条件下的ABS(一种无定形聚合物)没有表现出这种差异。
模具热膨胀补偿补偿重要性在收缩计算时已得到证明。这一点对确定塑料工具绝对收缩值及金属工具的更多扩展至关重要。在确定零件绝对收缩值时若忽略了模具生产塑件的热热膨胀将导致重大错误。
不同液晶高分子零件具有不同缺点,需使用相应的补偿。实验表明,这种液晶高分子材料的收缩取决于工艺条件。收缩问题只发生在工件被加工的情况下。因此,常规的收缩分析是不行的,使用立体成型的工具,还需要其他技术加以补偿。
非晶体聚合物的收缩不会受模具材料类型及冷却条件的影响。因此,如有可能,因此建议使用SL模具加工时材料优先使用无定形聚合物。
参考文献:
[1]P.D.Hilton,P.F.Jacobs,RapidTooling:TechnologiesandIndustrialApplications,Marcel Dekker,2000.
[2]T.Luck,F.Baumann,U.Baraldi,Comparison of downstreamtechniques for functional and technical prototypes—fast toolingwith RP,Proceedings of Fourth European RP Conference,13–15 June,1995,Belgriate,Italy,pp.247–260.
[3]J.Eschl.Experiences with photopolymer inserts for injectionmoulding,European Stereolithography Users Group meeting,2–5 November,Florence,Italy,1997.
[4]R.A.H arris. Direct AIM tooling. Rapid prototyping& tooling state of the industry annual worldwide progress report,WohlersReport 2002,Published by Wohlers Associates Inc,USA,Part 3:Tooling,p.70,2002.
[5]A.Schulthess,B.Steinmann,M.Hofmann,Cibatool?SL epoxyresins and some new applications.Proceedings of the 1996 NorthAmerican Stereolithography Users Group Meeting,10–14 March,San Diego,CA,1996.
[6]M.Damle,S.Mehta,R.Malloy,S.McCarthy,Effectoffibreorientationon the mechanical propertiesofannjectionmoldedpartandastereolithography-insertmoldedpart.ProceedingsoftheSocietyofPlasticsEngineers(SPE)AnnualTechnicalConfer-ence(ANTEC),Atlanta,GA,pp.584–588,1998.
[7]D.A.Velarde,M.J.Yeagley,Linearhrinkageifferencesininjectionmouldedparts,PlasticsEngineering,TheSocietyofPlasticsEngineers,December 2000,pp.60–64,2000.
[8]P.Gipson,P.Grelle,B.Salamon,The effects of process conditions,nominal wall thickness,and flow length on the shrinkagecharacteristics of injection molded polypropylene,The Journal of Injection Molding Technology 3(3)(1999)117–125.
[9]P.Patel,Effect of processing conditions on the shrinkage andcrystallinity of injection moulded parts,Proceedings of theSociety of Plastics Engineers(SPE)Annual Technical Conference(ANTEC),Toronto,Canada,pp.3632–3635,1997.
[10]D.Tursi,S.P.Bistany,Process and tooling factors affecting sinkmarks for amorphous and crystalline resins,Journal of InjectionMolding Technology 4(3)(2000)114–119.
[11]D.Pierick,R.Noller,The effect of processing conditions onshrinkage.Proceedings of the Society of Plastics Engineers(SPE)
Annual Technical Conference(ANTEC),Montreal,Canada,pp252–253,1991.
[12]BS EN ISO 294-1.Plastics—injection moulding of test speci-mens of thermoplastic materials—Part 1:General principles,andmoulding of multipurpose and bar test specimens,British Standards Institution,Issue 2,ISBN 0 580 27299 0,1998.
[13]BS EN ISO 294-4.Plastics—injection moulding of test speci-mens of thermoplastic materials—Part 4:Determination ofmoulding shrinkage,British Standards Institution,Issue 2,ISBN0 580 27826 3,1998.
[14]ASTM D955,Standard test method for measuring shrinkage frommold dimensions of molded plastics,American Society for Testing and Materials,1996.
[15]R.A.Harris,N.Hopkinson,H.Newlyn,R.Hague,P.M.DickensLayer thickness and draft angle selection for stereolithographynjection mould tooling,International Journal of ProductionResearch 40(3)(2002)719–729.
[16]R.A.Harris,H.A.Newlyn,P.M.Dickens,The selection of moulddesign variables in direct stereolithography injection mould tooling,Journal of Engineering Manufacture,IMechE Proceedings part B 216(B4)(2002)499–505.
[17]BS EN ISO 291.Plastics—standard atmospheresforconditioningand testing,British Standards Institution,ISBN 0 580 28585 5,1997.
[18]Machine Design,1993,1994 Materials Selector Issue.Vol.65,No.26,December,Penton Publishing Inc.
[19]A.W.Birley,R.J.Heath,M.J.Scott,PlasticsMaterials:PropertiesandApplications,second ed.,Blackie&Son Limited,1988.
[20]H.Belofsky,Plastics:Product Design and Process Engineering,Carl Hanser Verlag,ISBN 1-56990-142-2,1995.
[21]D.M.Bryce.Plastic Injection Moulding…material selection andproduct design fundamentals.Society of Manufacturing Engineers,ISBN 0-87263-488-4,1997.
[22]MatWeb.The Online Material Information Resource Homepage.
http://www.matweb.com/index.asp?ckck=1
[23]A.J.Munday,R.A.Farrar,An Engineering Data Book,Macmillan Press Ltd,ISBN 0 333 258290,1979.